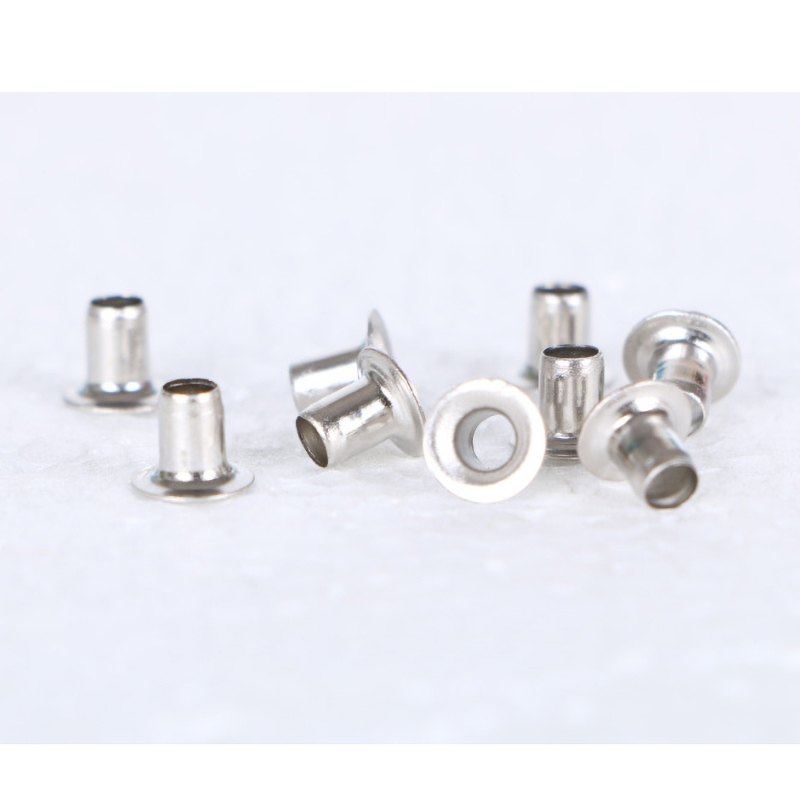
Hollow Tubular Rivets
- Product Information
Hollow Tubular Rivets are mechanical fasteners used to connect materials. They have a hollow tubular structure with a head at one end and a hollow tail at the other end. This design requires less force to install while providing strong connection strength.
Product Features
Hollow Tubular Rivets have the following features:
1. Lightweight Design
Lightweight: The hollow structure significantly reduces the weight of the rivet, making it suitable for weight-sensitive applications.
Material Selection: Lightweight materials such as aluminum, brass, and stainless steel are usually used.
2. High-Strength Connection
Strength-to-Weight Ratio: Despite its light weight, its strength is not reduced and it can withstand high shear and tension forces.
Uniform Stress: The hollow design can evenly distribute stress during installation and reduce stress concentration.
3. Easy to Install
Easy to install: During installation, you only need to pre-drill holes in the material and then deform the tail with a rivet gun or hand tool to form a strong connection.
Low installation force: The force required for installation is only about 25% of that of solid rivets, reducing the requirements for installation tools.
4. Material adaptability
Multiple materials: It can be made of steel, stainless steel, aluminum, brass, copper and other materials to suit different application requirements.
Surface treatment: It can be galvanized, nickel-plated, anodized and other surface treatments to enhance corrosion resistance.
5. Flexible design
Multiple specifications: A variety of sizes, head shapes (such as flat head, round head, countersunk head, etc.) and lengths are available.
Customization: Special sizes and shapes can be customized according to customer needs.
6. Durability
Vibration resistance: It can maintain a stable connection under high vibration environment.
Corrosion resistance: Especially aluminum and stainless steel rivets have good corrosion resistance.
Application scenarios
Hollow Tubular Rivets are widely used in multiple industries and solve various connection problems:
1. Automotive industry
Lightweight: Used for the connection of body parts, interior and engine parts, it helps to reduce vehicle weight and improve fuel efficiency.
High-strength connection: Provides reliable connection in key components such as braking systems and suspension systems.
2. Electronics industry
Non-conductive connection: Used for assembly of electronic equipment housing to avoid short circuit risks.
Lightweight and aesthetics: Provides compact and aesthetic connections in thin and light devices.
3. Leather products
Aesthetics and durability: Used for decorative connections of belts, handbags, shoes, etc., providing an aesthetic and durable appearance.
Lightweight: Reduce product weight and improve wearing comfort.
4. Construction industry
Lightweight structure: Used for connection of lightweight building components, such as decorative metal frames.
Corrosion resistance: In outdoor environments, stainless steel and aluminum rivets can resist corrosion.
5. Aerospace
High strength and lightweight: Provides high-strength connection and reduces weight in aircraft structures and interior components.
Vibration resistance: Remains stable in high vibration environments.
Care and maintenance
1. Post-installation inspection
Check the connection: After installation, check whether the rivets are firm and ensure that they are not loose or not completely deformed.
Appearance inspection: Check the surface of the rivet for scratches or damage, and repair if necessary.
2. Anti-corrosion measures
Regular inspection: In a corrosive environment, regularly check the corrosion of the rivets and replace them if necessary.
Surface protection: For rivets that are prone to corrosion, anti-corrosion coatings can be applied or anti-corrosion washers can be used.
3. Cleaning
Cleaning method: Use a soft cloth and mild detergent to clean the surface of the rivet, and avoid using corrosive chemicals.
Remove dirt: Regularly remove dirt and debris around the rivet to prevent corrosion.
FAQs
1. Are Hollow Tubular Rivets lighter than solid rivets?
Yes, Hollow Tubular Rivets weigh significantly less than solid rivets due to their hollow design.
2. How much force is required to install Hollow Tubular Rivets?
The force required for installation is only about 25% of that of solid rivets, which reduces the difficulty of installation.
3. Can the size of Hollow Tubular Rivets be customized?
Yes, Hollow Tubular Rivets can be customized in different sizes and shapes according to customer needs.
4. Are Hollow Tubular Rivets suitable for high vibration environments?
Yes, Hollow Tubular Rivets have good anti-vibration performance and are suitable for high vibration environments.
5. Is there an option for anti-corrosion coating?
Yes, Hollow Tubular Rivets can be surface treated with zinc plating, nickel plating, etc. to enhance corrosion resistance.
6. Are Hollow Tubular Rivets suitable for electronic devices?
Yes, Hollow Tubular Rivets can provide non-conductive connections and are suitable for the assembly of electronic devices.