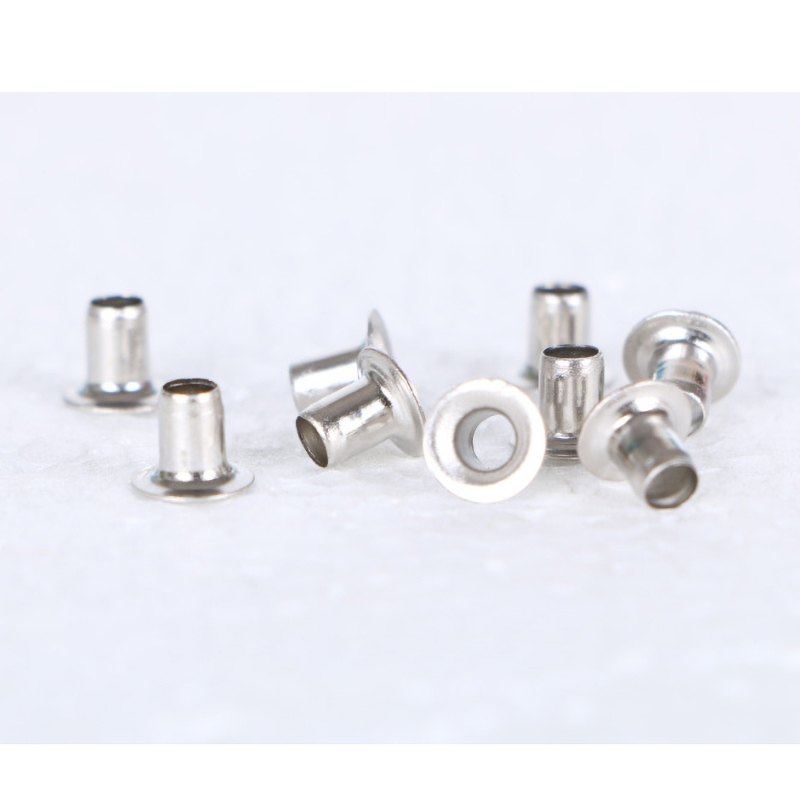
Full Tubular Rivets
- Product Information
Full Tubular Rivets are a standout in the world of fastening solutions as they are a dependable and sturdy way to join materials with strength and precision. Our Full Tubular Rivets have been designed to meet the highest quality standards for performance, making them popular across many industries. As for metal file accessories, it has to be mentioned that various types of our products exist in this category. Different rivets in this category are tailored for durability purposes.Both sides metal rivets range from small delicate assembly ones to large heavy structural ones, leaving no gap unfilled and having well defined goal.
The China Full Tubular Rivets employ superior materials which make them not only strong but also corrosion resistant thus they can serve for an extended period without breaking down. These types of rivets are ideal for use in extreme environments where other fasteners might fail.Metal file accessories from us are multipurpose. It doesn’t matter whether you are dealing with metallic, wooden or plastic surfaces; our rivets will work perfectly on all these materials. They are recommended due to their ease of fixing and strong grip thereby making them suitable even for commercial usage and industrial fields.
Full Tubular Rivets Sizes:
Standard Sizes
Custom Dimensions
Graduated Sizes
Metric and Imperial
Fine Threads
Coarse Threads
Panel Sizes
Miniature Rivets
Technical process of Full Tubular Rivets
1. Material selection
The manufacturing materials of Full Tubular Rivets mainly include:
Aluminum and aluminum alloys: lightweight, corrosion-resistant, suitable for aviation, electronics and other fields.
Steel (carbon steel or stainless steel): high strength, widely used in machinery manufacturing and automotive industries.
Copper and copper alloys: good conductivity, used for electronic equipment connection.
2. Manufacturing process
1. Cold forging: The metal wire is pressed into a hollow tubular rivet through a cold forging process to ensure dimensional accuracy and strength.
2. Heat treatment (for steel rivets): improve the hardness and durability of the rivet.
3. Surface treatment: including galvanizing, anodizing, painting, etc. to enhance corrosion resistance.
3. Structural features
Hollow tubular design: The main body of the rivet is hollow to reduce the overall weight.
Various head styles: including round head, flat head, countersunk head, etc. to meet different connection requirements.
The tail is deformable: during installation, the tail is expanded by mechanical or manual tools to form a firm connection.
Features and advantages of Full Tubular Rivets
1. Lightweight: The hollow structure makes it less heavy than solid rivets, which is suitable for applications where weight reduction is required.
2. Easy installation: It can be quickly installed by manual or pneumatic rivet guns, especially suitable for mass production.
3. Good seismic performance: Suitable for environments with large vibrations, such as cars and aircraft.
4. Wide range of applications: It can be used to connect a variety of materials such as metal, plastic, and leather.
5. High shear strength: Steel Full Tubular Rivets can withstand large shear forces and are suitable for high-load structures.
Application scenarios of Full Tubular Rivets
1. Automobile manufacturing
Widely used in automobile bodies, interiors, chassis and other parts. For example:
Connection between the roof and the body: Use lightweight rivets to reduce the weight of the entire vehicle.
Bumper fixation: Avoid deformation caused by welding and improve assembly accuracy.
Door hinge installation: ensure long-term reliability.
2. Aerospace
Due to the light weight and high strength of Full Tubular Rivets, this type of rivet is widely used in the manufacture of aircraft and spacecraft. Typical applications include:
Wing skin connection: reduce air resistance during flight.
In-cabin equipment fixation: strong earthquake resistance to ensure stable operation of equipment.
Fuel tank seal: corrosion-resistant material to prevent chemical erosion.
3. Electronic and electrical industry
PCB board fixation: copper rivets are used for ground connection of electronic equipment.
Home appliance shell assembly: such as metal parts connection of washing machines and refrigerators.
4. Architecture and decoration
Metal curtain wall splicing: beautiful and weather-resistant.
Aluminum alloy door and window installation: improve structural stability.
5. Military and ships
External armor fixation of armored vehicles: impact resistance and high strength.
Ship deck riveting: salt spray corrosion resistance to ensure long-term use.
6. Furniture manufacturing
Metal furniture connection: such as the combination installation of office desks and shelves.
Leather and metal fixation: suitable for high-end furniture or luggage production.
Installation method and precautions of Full Tubular Rivets
1. Installation tools
Manual rivet gun: suitable for small batch operations.
Pneumatic rivet gun: suitable for high-efficiency production workshops.
Hydraulic riveting equipment: suitable for high-strength industrial riveting needs.
2. Installation steps
1. Pre-drilling: drill holes matching the rivet diameter on the material to be connected.
2. Insert rivets: pass the Full Tubular Rivets through the holes.
3. Fixing and riveting: Use the rivet tool to tighten the tail to expand and lock it.
4. Check and adjust: Make sure the rivet is firm, without looseness or deformation.
3. Precautions
Hole diameter matching: Too large a hole will result in loose riveting, and too small a hole will be difficult to insert.
Material adaptation: Hard materials (such as stainless steel) require higher strength rivets.
Anti-corrosion treatment: In humid or corrosive environments, you should choose rivets with coating protection.
Full Tubular Rivets FAQ:
What is the difference between Full Tubular Rivets and Semi-Tubular Rivets?
Full Tubular Rivets are completely hollow rivets, suitable for lightweight material connections, and the entire tail expands and fixes during installation.
Semi-Tubular Rivets are only partially hollow at the tail, which is more suitable for thick material connections and has higher strength.
Will Full Tubular Rivets easily loosen in a vibrating environment?
No. Since rivets expand and lock after installation, they are more resistant to vibration than screws or nuts, and are suitable for high-vibration environments such as automobiles and aerospace.
Are metal rivets suitable for plastic materials?
Yes, certain types of metal rivets, such as those with a soft grip or designed for use with plastic, can be used to join plastic materials without causing damage.
What is the difference between a solid and a blind rivet?
Solid rivets require access to both sides of the materials for installation, while blind rivets can be set from one side using a special tool that pulls the rivet through and sets it in place.
Can you use metal rivets in woodworking?
Metal rivets can be used in woodworking for applications such as attaching metal hardware to wooden structures or for decorative purposes.